From Research to Process Design
GTK’s mineral processing unit provides mining companies ore beneficiation studies for assessing ore deposits and drawing up profitability calculations, from preliminary laboratory testing and to campaigns at GTK’s pilot plant.
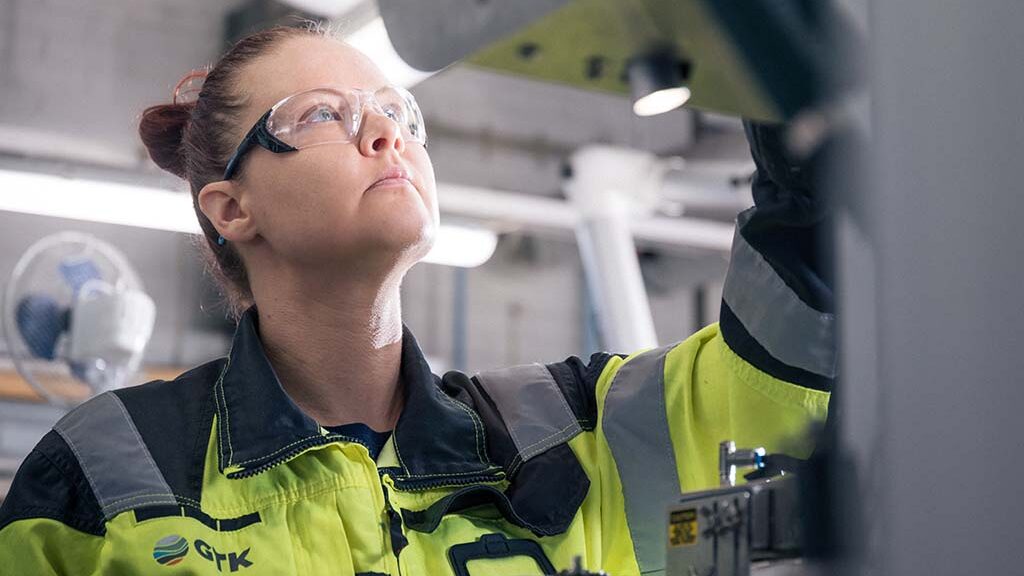
Our research portfolio includes thorough mineralogical studies for ore and concentrates as well as chemical analyses, and our research reports are made available for clients to use in their ore deposit profitability studies.
When necessary, we assist our customers in the basic design of processes, which typically includes process chart preparation, equipment dimensioning, the evaluation of operation and investment costs and a layout plan. The initial data for design is usually obtained with a pilot run using the materials provided by the customer. A preliminary design can also be made case by case with the results from laboratory testing or a minipilot run.
Over time, our studies have included a wide range of different ores and other material, the most central ones being:
- Gold ore
- Platinum (PGM) ore
- Nickel and nickel-copper ore
- Porphyry copper ore
- Complex sulphide ore (Cu, Zn, Pb)
- Phosphates
- Iron ore
- Industrial minerals (talc, calcite, ilmenite, anorthosite, pegmatite, etc.)
- Diamond ore
- Metallurgic dregs and slag
- Recycling material and contaminated soil
- Coal
The composition and structure of ores, other raw materials, and processed products are studied with chemical analytics and mineralogical surveying. In mineralogical surveys, GTK uses a modern mineral liberation analyser (MLA) connected to an electron microscope, other types of microscopes (photo-optic, fluorescence-based and IR-based), an x-ray diffractometer, and other necessary equipment. If necessary, precious metals of low concentration (Au and PGMs) can be concentrated by means of hydro or heavy liquid separation before the preparation of samples for microscopic study.
Our laboratory activities include grinding tests (autogenous grinding included) and beneficiation tests utilising a variety of methods (flotation, magnetic separation, specific weight separation, and heavy medium separation). Hydrometallurgical testing methods include acid leaching, pressure leaching and cyanidation (gold ores). Furthermore, we have recently been focused on using bioleaching for extracting metals from ores and slag. We also have equipment for beneficiation and leaching product thickening and filtering tests. For laboratory studies, samples (usually drill cores) ranging from a couple of dozen kilograms to several hundred kilograms are needed.
The initial data required in process design and profitability calculations can be most reliably obtained from a pilot study. For a pilot run, approximately 50–300 tonnes of samples are needed, sometimes up to a couple of thousand tonnes. The required feeding capacity for crushing is 10–40 tonnes per hour and 0.5–5 tonnes per hour in the grinding/beneficiation circuit.
Our pilot plant includes a versatile selection of equipment for all unit processes, such as crushing, homogenisation, grinding, classification, flotation, magnetic separation, specific weight separation, heavy medium separation, thickening, and filtering. We have modern a set of instruments and a process computer for process control and the collection of measuring data. We use an online analyser to measure basic metal concentrations directly from slurry flows.
Our minipilot system, built inside a transport container, is an alternative for continuous test runs, and the sample size required for a minipilot run is 0.5–2 tonnes. The minipilot system’s equipment includes a grinding/classification circuit and a flotation circuit with the feeding capacity of 10–50 kilograms per hour. The minipilot container can also be taken for a test run to an already existing plant.