Science Blog: Substitution of Cement with Slag in Cemented Paste Backfill (CPB): Evaluation of Technical and Environmental Properties
Cemented paste backfill (CPB) is a support and filler material used in underground mine cavities. It offers an environmentally sustainable way to utilize extractive wastes, one of the largest waste streams in the world. CPB consists of mine tailings, water and binder material, which is usually cement. Replacing cement with secondary raw materials such as granulated blast-furnace slag strengthens the internal microstructure of the CPB and reduces the total CO2 emissions.
Research on cemented paste backfill (CPB) materials is a new field of investigation for GTK. The topic has been studied since 2019 in the EDRF-funded Kove-Pro project in close co-operation with Savonia University of Applied Sciences (Savonia) and industrial partners.
The project has now proceeded to the publishing phase. This blog post presents the results of the first characterization study (Solismaa et al. 2021).
Sample preparation
Five CPB recipes with various binder mixtures were designed (R1–R5, Table 1) to find an optimal recipe in which the cement is either replaced or partly substituted with slag.
Table 1. Quantities of starting materials for the cemented paste backfill recipes R1–R5.
Starting Materials | Cemented paste backfill recipe (cement:slag ratio) | ||||
R1 (40:60) | R2 (50:50) | R3 (0:100) | R4 (100:0) | R5 (50:50) | |
Mine tailings (%) | 63 | 63 | 63 | 63 | 65 |
Water tot. (%) | 30 | 30 | 30 | 30 | 30 |
Share of pore water (%) | 96 | 96 | 96 | 96 | 100 |
Share of process water (%) | 4 | 4 | 4 | 4 | 0 |
Binder (%) | 7 | 7 | 7 | 7 | 5 |
Share of cement in binder (%) | 40 | 50 | 0 | 100 | 50 |
Share of slag in
binder (%) |
60 | 50 | 100 | 0 | 50 |
Consistency slump (mm) | 200 | 220 | 210 | 190 | 200 |
The specimens (test blocks) were prepared according to the recipes and cured for 60 days in a climate test chamber before testing and measurements. Figure 1 illustrates the opening of a CPB mould and settings of the unconfined compressive strength measurements at Savonia.
Results
The compressive strength test results indicated that partial substitution of cement (samples R1 and R2) with slag improved the compressive strength of CPB (see Figure 2). Total replacement of cement with slag (R3) reduced the early strength but gave good strength properties in the later phase, achieving the same level of strength as the cement-only recipe (R4) in 56 days. This suggests that total cement replacement with slag could be possible for applications where rapid curing is not required.
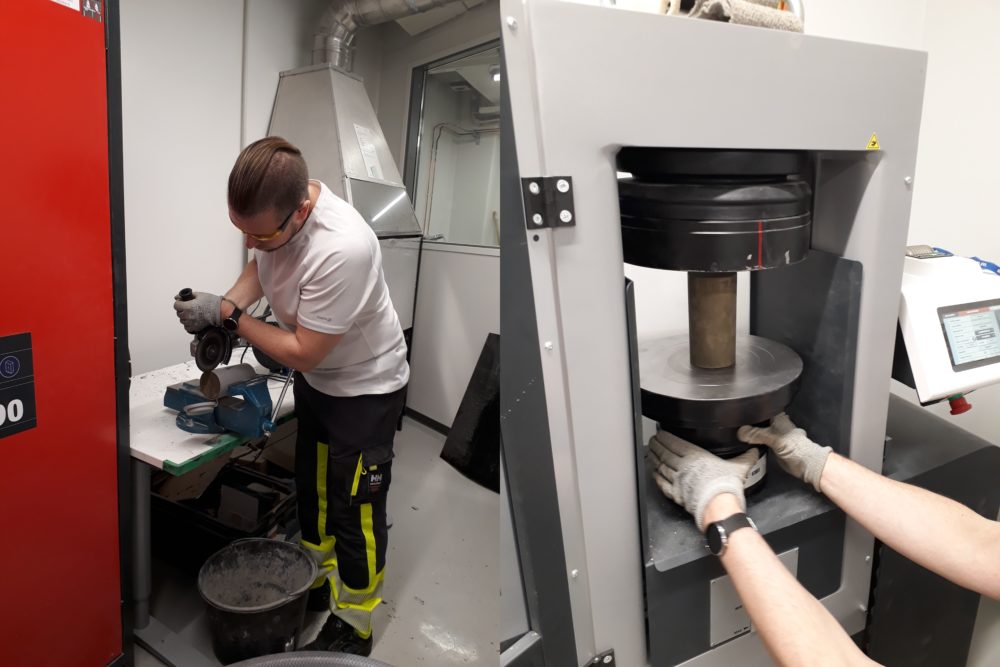
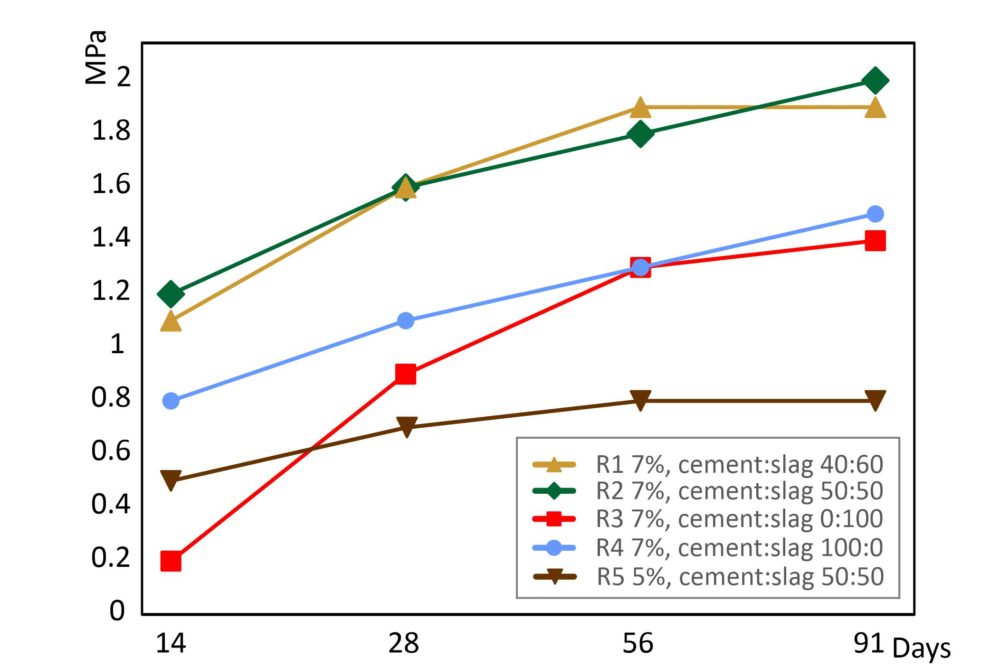
Mineralogical and chemical analyses demonstrated that the mine tailings and CPB specimens used in the study contained approximately 2% of sulphur, which was mainly bound to the calcium sulphate mineral gypsum. Gypsum was also present in the cement used in the study. The water used for CPB preparation, obtained from the mine, also had a relatively high content of sulphate.
Slag needs an activator such as cement to act as a hardener. However, no activator was added in the CPB specimen in which only slag binder was used (R3). The activator was presumably gypsum present in the parent materials. The hydration product ettringite (Figure 3) was detected from all CPB specimens and its content was lowest in the slag-containing specimens. This indicates that the replacement of cement with slag inhibited the formation of ettringite. C-S-H gel, the main binding agent in concrete, was possibly formed as a result of reactions between the hydrated lime of cement and slag, explaining the good strength properties of slag and cement-containing samples.
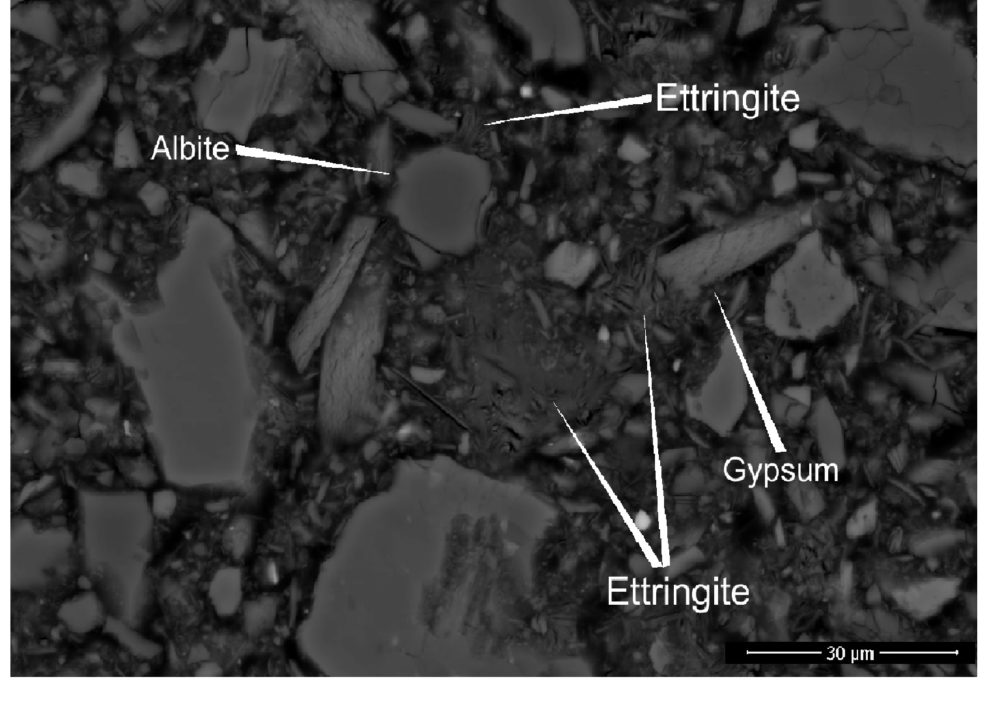
Leaching tests revealed increased leaching of As in water when the ground CPB specimens were compared with ground mine tailings samples. Leaching was connected with the rising pH caused by the addition of cement and slag. A further study using whole CPB specimens and actual mine water as a solvent has been implemented to enable conclusions on what reactions would occur in an actual mine setting. The results of these tests will be published later.
X-ray tomography revealed a vertically differentiated density structure in the CPB samples (Figure 4). The lower parts of all samples were denser in comparison with the upper parts of the specimens. The possible cause of this is probably connected to the compaction of solid particles in the base and upward injection of the liquid phase. More research is needed to determine why this phenomenon occurs and what consequences it has for the placement of CPB in mine voids. The porosity results obtained using X-ray tomography had two clear standouts. The sample with pure slag binder (R3) was by far the least porous, and the sample with pure cement binder (R4) was the most porous.
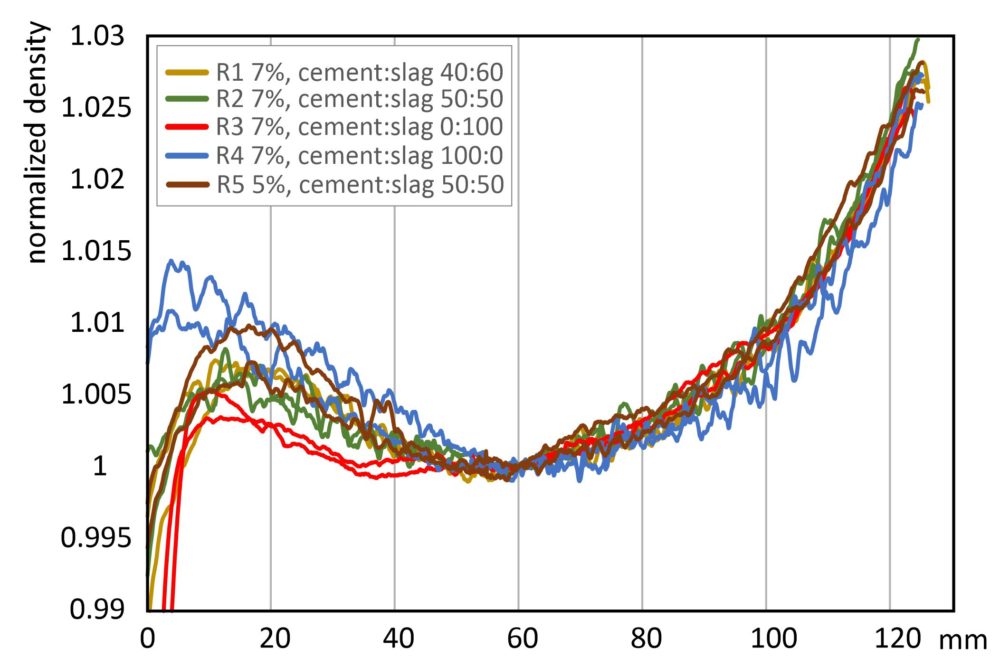
Conclusions
The results indicate that partial substitution of cement with slag lowers the porosity and enhances the strength properties of CPB. Even total replacement of cement with slag in CPB can be achievable. Since excess sulphate and ettringite are present in the system, sulphate attack might appear and affect the durability and leaching properties of CPB. However, this was not detected during the 91-day monitoring period of the compressive strength tests. Additional research is being conducted to determine the longer-term reactions between mine drainage water and CPB to enable conclusions on the stability of CPB in an actual mine setting.
The results of this study could be utilized in developing more durable and environmentally responsible CPB recipes for gold mines with a similar mineral composition and gold extraction method. For further details, please check the article recently published in Minerals.
Reference
Solismaa, S., Torppa, A., Kuva, J., Heikkilä, P., Hyvönen, S., Juntunen, P., Benzaazoua, M. & Kauppila, T. 2021. Substitution of Cement with Granulated Blast Furnace Slag in Cemented Paste Backfill: Evaluation of Technical and Chemical Properties. Minerals 2021, 11, 1068. Available at: https://doi.org/10.3390/min11101068
Text: Soili Solismaa and Tommi Kauppila
Soili Solismaa is a research scientist with over ten years of work experience at GTK. Her career began as a research assistant, and after graduation from Turku University’s Department of Geology, she started to work with issues concerning mining environments, especially the utilization of extractive waste. The Mining Environment and Recycling group is part of GTK’s Circular Economy Solutions unit, which promotes the efficient use of materials and reuse of mineral-based raw materials.
Tommi Kauppila is a Research Professor of Mine and Industrial Environments at GTK. He has worked with the environmental management and sustainability issues of mining at GTK for over fifteen years. His research interests include environmental risk assessment and management for mining operations, mine closure management, and sustainable mining.